Sifting screens play a crucial role in the manufacturing process by separating materials into different sizes and grades.
First Posted December 18, 2024 | Last Updated on July 30, 2025 by Ryan ConlonDisclosure: This Post Contains Affiliate Links; We earn a commission on purchases.
The use of the right sifting screen can enhance efficiency and quality in various industries, such as mining, aggregates, food processing, and pharmaceuticals.
Understanding the different types of sifting screens available is essential for selecting the most suitable option for specific applications.
There is a wide range of sifting screen types, each with its unique characteristics and applications.
Some popular varieties include vibratory screens, rotary screens, flip-flop screens, gyro screens, and air classifiers.
Manufacturers choose these options based on the specific needs of their industry, such as material type, desired particle size, and industry requirements.
Sifter screens are made from different materials and offer a variety of mesh screen variations and sieve screen options.
Depending on the material being processed, various screen opening sizes and sift screen materials are available.
These options allow manufacturers to optimize their sifting process and ensure efficient separation of materials.
Key Takeaways:
- The manufacturing process often requires sifting screens to separate materials into different sizes and grades.
- There are various types of sifting screens available, including vibratory screens, rotary screens, flip-flop screens, gyro screens, and air classifiers.
- The selection of the right sifting screen depends on factors such as material type, desired particle size, and industry requirements.
- Sifting screens offer benefits like high efficiency, low maintenance, and the ability to handle a wide range of materials.
- Manufacturers can choose from different mesh screen variations, sieve screen options, and screen opening sizes to optimize their sifting process.
Vibratory Screens
Vibratory screens, also known as vibratory screeners, are essential industrial screening machines used in various applications. These versatile vibrating screens are designed to separate materials based on size and density, ensuring efficient and accurate particle separation.
Industries such as mining, aggregates, battery manufacturing, metal powder manufacturing, food processing, and pharmaceuticals heavily rely on vibratory screens for their high efficiency and customizable features.
One of the key advantages of vibratory screens is their ability to handle a wide range of materials. From coarse aggregates to fine particles, these screens can effectively sieve and classify different material sizes. The use of multiple screens or meshes further enhances the efficiency of the screening process, allowing for precise separation according to desired specifications.
A notable example of advanced vibratory screening technology is the Hi-Sifter. This customizable vibrating screen offers superior performance, capable of achieving particle separation as fine as 10μm. With its high efficiency and fine particle separation capability, the Hi-Sifter is revolutionizing the industry by surpassing traditional vibratory machines.
Not only are vibratory screens highly efficient, but they also require low maintenance, making them cost-effective solutions for industrial screening needs. Their robust construction ensures durability and longevity, minimizing downtime and maximizing productivity.
Whether it’s for classifying aggregates, sifting metal powders, or separating ingredients in the food processing industry, vibratory screens provide reliable and customizable solutions for fine particle separation. The versatility, high efficiency, and durability of vibratory screens make them indispensable equipment in industrial applications.
Advantages of Vibratory Screens:
- High efficiency screens for efficient particle separation
- Customizable features to meet specific industry needs
- Wide range of material handling capabilities
- Low maintenance requirements for cost-effective operations
Applications of Vibratory Screens:
Industry | Application |
---|---|
Mining | Classifying aggregates |
Battery Manufacturing | Sieving and separating battery components |
Metal Powder Manufacturing | Sifting metal powders for quality control |
Food Processing | Separating ingredients for food production |
Pharmaceuticals | Screening pharmaceutical powders |
Rotary Screens
Rotary screens, also known as trommel screens, are highly effective for material separation based on size and shape. These screens are designed with a rotating drum or cylinder that is perforated with holes or meshes, allowing materials to pass through while separating them according to their size.
Rotary screens find extensive use in various industries, including mining, water treatment, agriculture, food processing, and waste management. Their versatility in handling a wide range of materials makes them a popular choice in the construction industry and beyond.
One of the key advantages of rotary screens is their high efficiency in material separation. The rotating drum ensures that materials of different sizes are effectively sorted and classified. This efficiency translates into improved productivity and cost savings for businesses.
Another benefit of rotary screens is their low maintenance requirements. The simple design and durability of these screens make them reliable and easy to maintain. Regular inspection and cleaning are typically all that’s needed to keep them operating optimally.
The wide range of materials that rotary screens can handle further enhances their appeal. Whether it’s gravel, sand, compost, or solid waste, these screens can efficiently separate and segregate the materials according to size, shape, or other characteristics.
Applications in the Construction Industry and Waste Management
In the construction industry, rotary screens play an essential role in material separation and recycling. They are commonly used to separate aggregates of different sizes during the production of concrete and asphalt. Additionally, these screens are utilized in waste management processes to separate recyclable materials from general waste, maximizing resource recovery and minimizing landfill waste.
Overall, the high efficiency, low maintenance requirements, and wide range of materials that rotary screens can handle make them invaluable tools in industries that rely on effective material separation. Whether it’s the construction industry or waste management, these screens offer a reliable and efficient solution for improving operational processes and overall productivity.
Flip-Flop Screens
Flip-flop screens, also known as flip-flow screens, are a perfect solution for separating difficult-to-screen materials like sticky or wet materials. These innovative screens use a series of flexible screens that flip back and forth to effectively deagglomerate and separate materials.
Flip-flop screens are widely used in industries such as mining, construction, waste management, and food processing. They offer high efficiency and low maintenance requirements, making them an ideal choice for various applications. These screens can efficiently handle a wide range of materials, including challenging ones that are difficult to screen using traditional methods.
One of the significant advantages of flip-flop screens is their ability to accurately control the particle size. This is particularly crucial in industries where precision is vital, such as food processing. From separating different sizes of grains to removing impurities from food products, flip-flop screens ensure a consistent and high-quality end result.
These screens also play a crucial role in waste management, efficiently separating and sorting recyclable materials from waste streams. The ability to effectively handle difficult materials and ensure proper waste segregation makes flip-flop screens an invaluable asset in waste management operations.
With their high efficiency, low maintenance requirements, and versatility in handling various materials, flip-flop screens are a popular choice for many industries. Whether it’s in mining, construction, waste management, or food processing, these screens deliver exceptional performance, enabling businesses to achieve their production goals effectively.
The Advantages of Flip-Flop Screens:
- Effective separation of difficult-to-screen materials
- High efficiency in handling a wide range of materials
- Accurate particle size control for enhanced product quality
- Low maintenance requirements for cost-effectiveness
- Application versatility across various industries
Flip-Flop Screens in Food Processing:
Flip-flop screens play a crucial role in food processing, ensuring the removal of impurities, separating grains of different sizes, and overall enhancing the quality and safety of food products.” – John Smith, Food Processing Expert
Flip-Flop Screens in Waste Management:
“The ability of flip-flop screens to efficiently separate and sort recyclable materials from waste streams is invaluable in waste management operations, contributing to a more sustainable and environmentally friendly approach.” – Sarah Johnson, Waste Management Specialist
Industry | Applications | Advantages |
---|---|---|
Mining | Ore sorting, scalping, dewatering | Efficient handling of challenging materials |
Construction | Demolition waste recycling, aggregate separation | Accurate particle size control |
Waste Management | Recyclable material separation, waste segregation | Low maintenance requirements |
Food Processing | Grain sorting, impurity removal | Enhanced product quality and safety |
Air Classifiers
Air classifiers play a crucial role in the mining and construction industries by enabling density-based separation of materials. These innovative machines utilize the power of air flow to separate lighter particles from heavier ones, ensuring efficient and precise material sorting.
In various mining operations, air classifiers are utilized to separate valuable minerals from unwanted gangue or waste materials. The density-based separation process allows for the efficient extraction of ore, maximizing production and reducing costs. Similarly, in the construction industry, air classifiers are used for separating different types of aggregates based on their density, ensuring the creation of high-quality construction materials.
An acclaimed air classifier in the industry is the Elbow Jet Air Classifier. Renowned for its superior performance, this cutting-edge classifier is highly effective in separating battery grade materials and other fine powders. With its advanced technology and precise air flow control, the Elbow Jet Air Classifier ensures optimal separation efficiency, even for materials with varying densities.
When it comes to handling materials with different density characteristics, air classifiers offer significant advantages. By utilizing the principles of density-based separation, these machines provide accurate and efficient sorting, ensuring that each material finds its rightful place in the process. With their invaluable contribution to various industries, air classifiers are essential for achieving optimized production and delivering high-quality products.
References
- https://www.goughengineering.com/en/articles/what-are-the-different-types-of-vibratory-screens-where-can-they-be-used
- https://elcanindustries.com/blog_posts/what-are-the-different-types-of-industrial-screening-equipment/
- https://www.powderbulksolids.com/screening-separation/sifters-critical-equipment-for-food-processing-30979
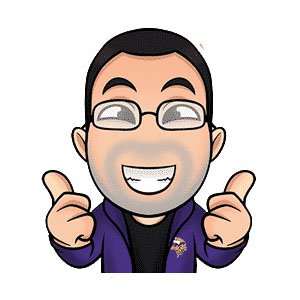
Meet Ryan Conlon, the passionate owner and driving force behind Pan for Treasure.
With an unwavering love for the art of gold panning, Ryan has transformed his enthusiasm into a thriving community hub for fellow treasure seekers. info@panfortreasure.com
A seasoned gold panning enthusiast, Ryan’s journey began with a simple pan and a dream, evolving into a deep appreciation for the history, geology, and thrill of uncovering precious metals.
Subscribe to Our Newsletter