Welcome to our guide on troubleshooting and fixing common issues with metal detectors.
First Posted November 26, 2024 | Last Updated on August 21, 2025 by Ryan ConlonDisclosure: This Post Contains Affiliate Links; We earn a commission on purchases.
In the food production industry, metal detectors are essential for ensuring the detection of metal contaminants and maintaining product safety.
However, these detectors can face various problems that can affect their performance.
It is crucial for companies to address these issues promptly to avoid costly product recalls and protect their reputation.
Key Takeaways:
- Understanding the common problems faced by metal detectors in the food production industry.
- Identifying the reasons behind detector malfunctions and inefficiencies.
- Implementing proper detector placement and suitable detection systems for different products and packaging.
- Addressing false signals and troubleshooting techniques to prevent unnecessary product waste.
- Exploring tips for preventing common issues and ensuring the proper functioning of metal detectors.
Common Reasons Why Your Metal Detector Is Not Working
When a metal detector is not working, it can be frustrating and impact your production line. There are several common reasons why this may occur, and understanding them is essential for prompt resolution. Here are some of the most prevalent detector problems and their corresponding solutions:
1. Use of Unsuitable Detection System
Using an inappropriate detection system for your specific production line can lead to inefficiency and inaccurate results. Different products and packaging require different types of detectors to ensure optimal performance. To resolve this issue, it is crucial to invest in the right detection system that matches the requirements of your line.
2. Improper Detector Placement
Improper detector placement can significantly affect its functionality. Using only a single detector at the end of the production line can result in missed detections and false signals. To address this, consider incorporating multiple detectors at strategic points along the line to enhance sensitivity and accuracy.
3. Interference from Surrounding Signals and Product Characteristics
Surrounding signals, such as electromagnetic fields, and product characteristics like moisture content, can interfere with the detector’s performance. To mitigate this issue, ensure that the detector is shielded from external signals and regularly calibrate it to account for any product-specific characteristics.
4. Ground Loops
Ground loops occur when two pieces of metal within the detector’s range touch each other, resulting in false signals and unnecessary product rejections. To overcome this problem, implement proper grounding techniques and ensure that metal objects within the detector’s range are adequately separated.
5. Lack of Training on Operating and Maintaining Equipment
Proper training on operating and maintaining metal detectors is essential to prevent handling errors and mistakes that can impact their functionality. Ensure that your staff receives thorough training on detector operation, routine maintenance, and troubleshooting techniques.
To summarize, addressing common detector problems is crucial for maintaining the efficiency and reliability of metal detection systems. By employing suitable detection systems, ensuring proper placement, minimizing interference, eliminating ground loops, and providing comprehensive training to operators, you can effectively resolve detector issues and ensure accurate contaminant detection.
Image:
Common Detector Problems | Solutions |
---|---|
Use of an unsuitable detection system | Invest in the right detection system for your production line |
Improper detector placement | Incorporate multiple detectors at strategic points along the line |
Interference from surrounding signals and product characteristics | Shield the detector from external signals and calibrate it regularly |
Ground loops | Implement proper grounding techniques and separate metal objects |
Lack of training on operating and maintaining equipment | Provide comprehensive training to operators |
Food Metal Detector Troubleshooting: Three Main Causes of False Signals
False signals in food metal detectors can have significant consequences, leading to product waste and lost profits. Understanding the main causes of false signals and implementing effective troubleshooting techniques is essential for maintaining efficient detector performance and optimizing food production processes.
1. Interference
One of the primary causes of false signals in food metal detectors is interference from nearby machines that emit radio waves or high vibrations. These external factors can disrupt the detector’s ability to accurately detect metal contaminants, resulting in unnecessary product rejections or false acceptances.
To mitigate interference-related issues, it is crucial to:
- Ensure proper spacing between different machines to reduce the impact of radio waves and vibrations.
- Invest in shielding materials or techniques to minimize the influence of external electromagnetic interference.
2. Lack of Uniformity in Product Characteristics
Another common cause of false signals is the lack of uniformity in product characteristics. Variations in temperature, humidity, or other properties can trigger the metal detector to produce false alerts, leading to unnecessary product waste.
To address this issue, companies can:
- Implement proper product conditioning techniques to maintain consistent temperature and humidity levels.
- Regularly calibrate and adjust the metal detector’s sensitivity settings based on the specific product characteristics.
3. Conveyor Issues
The conveyor system plays a crucial role in the proper functioning of food metal detectors. However, issues within the conveyor system can contribute to false signals and rejections.
To prevent conveyor-related detector problems, it is important to:
- Maintain regular maintenance and cleaning of the conveyor system to prevent metal fragments from accumulating.
- Ensure proper alignment and calibration of the conveyor belt to avoid causing false signals.
By addressing these three main causes of false signals, food manufacturers can minimize unnecessary product waste, optimize product quality, and maximize the efficiency of their metal detection systems.
Issue | Troubleshooting Technique |
---|---|
Interference | Ensure proper spacing between machines to reduce interference. Invest in shielding materials or techniques. |
Lack of Uniformity in Product Characteristics | Implement proper product conditioning techniques. Regularly calibrate and adjust sensitivity settings. |
Conveyor Issues | Maintain regular maintenance and cleaning of the conveyor system. Ensure proper alignment and calibration of the conveyor belt. |
Implementing these troubleshooting techniques and best practices can help food manufacturers maintain efficient and accurate metal detection, ensuring the safety and quality of their products.
Four Tips for Preventing Food Metal Detector Issues
While occasional issues with metal detectors cannot always be avoided, there are steps companies can take to prevent common problems. By following these preventative measures, you can ensure that your detectors are operating at their best and minimize the risk of any disruptions in your production line.
- Control the Environment: Maintaining consistent temperature and humidity levels is crucial for detector performance. Fluctuations in these factors can affect the accuracy of metal detection. Make sure to monitor and control the environment in which your detectors are operating.
- Invest in the Right Detection System: Having a detection system that is suitable for your specific products and packaging is essential. Different products may require different types of detectors, so ensure that you have the appropriate system in place to achieve optimal results.
- Regular Maintenance: Proper maintenance is key to keeping your detectors in good working condition. Follow the manufacturer’s recommended schedule for maintenance tasks such as cleaning, calibration, and component checks. By staying proactive, you can catch any potential issues before they escalate.
- Consult the Manufacturer: If you encounter any issues or have questions about your metal detectors, don’t hesitate to reach out to the manufacturer. They have the expertise and knowledge to provide guidance, troubleshooting tips, and solutions to help resolve any problems that may arise.
By implementing these tips, you can ensure that your metal detectors are operating efficiently and effectively, reducing the risk of false rejections and product recalls. Taking the necessary precautions now can save you time, money, and maintain the integrity of your food production process.
Conclusion
Troubleshooting and addressing common issues with metal detectors is essential for maintaining their efficiency and effectiveness. By understanding the underlying causes of detector problems and implementing best practices such as proper detector placement, suitable detection systems, and regular maintenance, companies can prevent costly issues and ensure the safety and quality of their products. Consulting experts from the manufacturer can provide valuable insights and support in solving any problems that may arise, allowing companies to take a proactive approach to detector troubleshooting. This proactive approach helps minimize downtime and maximize productivity in production facilities.
Fixing detector issues requires a comprehensive understanding of the factors that can affect performance, such as interference, product characteristics, and conveyor problems. By actively addressing these issues, manufacturers can prevent false signals and minimize product waste, ultimately protecting their profits and reputation in the market.
In summary, adopting detector troubleshooting tips and strategies is crucial for maintaining optimal detector performance. By investing in training, proper maintenance, and consulting with experts, companies can resolve common issues, minimize downtime, and ensure smooth operations in the food production industry. By prioritizing detector maintenance and troubleshooting, manufacturers can maintain their competitive edge and provide safe, high-quality products to the market.
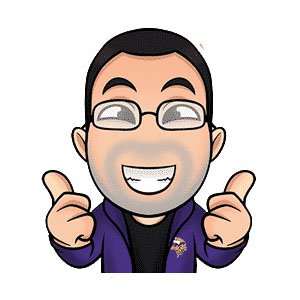
Meet Ryan Conlon, the passionate owner and driving force behind Pan for Treasure.
With an unwavering love for the art of gold panning, Ryan has transformed his enthusiasm into a thriving community hub for fellow treasure seekers. info@panfortreasure.com
A seasoned gold panning enthusiast, Ryan’s journey began with a simple pan and a dream, evolving into a deep appreciation for the history, geology, and thrill of uncovering precious metals.
Subscribe to Our Newsletter