Sifters and classifiers are essential equipment in various industries, serving purposes such as safety screening, scalping, classifying, and de-dusting.
First Posted December 21, 2024 | Last Updated on July 29, 2025 by Ryan ConlonDisclosure: This Post Contains Affiliate Links; We earn a commission on purchases.
To ensure optimal performance and reliability, it is crucial to implement proper maintenance practices. In this article, we will explore maintenance tips and best practices for sifters and classifiers.
Key Takeaways:
- Regular maintenance enhances the performance and reliability of sifters and classifiers.
- Implementing preventive maintenance ensures the integrity of the production process and prevents accidents during safety screening.
- Proper troubleshooting and maintenance are crucial for effective scalping and achieving precise particle size control.
- Maintaining efficient classifying operations and consistent product quality requires adherence to classifier maintenance guidelines.
- Efficient de-dusting operations rely on proper cleaning techniques and preventing material build-up in sifters and classifiers.
Safety Screening: Ensuring Process Integrity
Safety screening plays a critical role in industries that process dry materials, employing centrifugal sieves as a reliable method. Its primary objective is to establish a protective barrier between the input of a production process and downstream equipment by eliminating hazardous objects and tramp materials. To maintain the integrity of the production process and prevent catastrophic incidents, it is crucial to implement regular preventive maintenance for sifters and classifiers.
Safety screeners are subject to wear and tear due to the nature of their operation. Regular maintenance ensures that the equipment operates at its optimal performance levels, maximizing efficiency and minimizing downtime. By adhering to preventive maintenance procedures, you can identify and rectify potential issues before they escalate, guaranteeing smooth production processes and ensuring the safety of your workforce.
Please refer to the table below for a summary of key preventive maintenance tasks for safety screeners:
Preventive Maintenance Task | Frequency |
---|---|
Inspect and clean screens | Weekly |
Check for loose connections | Monthly |
Lubrication of moving parts | Quarterly |
Replace worn-out components | As needed |
Implementing these preventive maintenance tasks will significantly contribute to the overall performance, reliability, and safety of your sifters and classifiers, enabling you to achieve uninterrupted production processes and exceptional product quality. Remember, when it comes to safety screening, preventive maintenance is key.
https://www.youtube.com/watch?v=ECaBPJbh_iE
Scalping: Achieving Particle Size Control
Scalping is a vital process in bulk material production, involving the removal of a small percentage of particles from the top end of the particle size distribution curve. This technique allows for precise control over the particle size distribution, enabling industries to meet specific product requirements.
However, the effectiveness of scalping operations heavily relies on the proper maintenance and troubleshooting of sifters. Ensuring that your sifters are in optimal condition is crucial for achieving the desired particle size control. Regular maintenance activities such as inspection, cleaning, and troubleshooting play a significant role in enhancing the efficiency of scalping operations.
When it comes to sifter troubleshooting, it is essential to identify and address any issues promptly. Common problems that may arise during scalping include blockages, excessive vibrations, and erratic operation. By troubleshooting these issues, downtime can be minimized, and the consistent and accurate separation of particles can be maintained.
In terms of sifter maintenance, regular cleaning is key to preventing any material buildup that may hinder the scalping process. This includes the cleaning of screens, internal components, and discharge outlets. Additionally, lubricating moving parts and inspecting for wear and tear are important preventive measures to keep your sifters operating smoothly.
By incorporating comprehensive maintenance strategies and effective troubleshooting techniques, you can ensure the efficient and reliable performance of your sifters during scalping. This will ultimately contribute to the production of high-quality materials and the overall success of your operations.
Common Scalping Issues | Troubleshooting Steps |
---|---|
Blockages in the sifter screens | 1. Stop the sifter and power off the equipment 2. Check for blockages by inspecting the screens and discharge outlets 3. Remove any accumulated material using appropriate tools 4. Restart the sifter and ensure smooth operation |
Excessive vibrations during scalping | 1. Check for loose or damaged components 2. Tighten or replace any faulty parts 3. Ensure proper alignment of screens and drive mechanisms 4. Balance the sifter if necessary |
Erratic operation and inconsistent particle separation | 1. Inspect the screens for damage or clogging 2. Clean or replace damaged screens as needed 3. Adjust the sifter settings to achieve the desired particle separation 4. Monitor the sifter during operation and make necessary adjustments |
By following these troubleshooting and maintenance practices, you can optimize the performance of your sifters and achieve precise particle size control during the scalping process.
Classifying: Creating Multiple Grades of Material
Classifying is a crucial process used in various industries, including agriculture, to produce materials with different grades. By separating particles based on their size using screens of different sizes, classifying enables the creation of multiple grades of material, such as lime powders for agricultural applications.
To ensure efficient classifying operations and consistent product quality, it is essential to follow proper classifier maintenance guidelines. Regular inspections play a vital role in identifying and addressing issues that may affect the performance of the classifier.
“Regular inspections help ensure that the screens are in good condition and properly aligned. Any damages or misalignments can significantly impact the accuracy and efficiency of the classifying process.”
In addition to inspections, regular cleaning of the classifier is crucial. Over time, particles can accumulate on the screens, reducing their effectiveness and potentially leading to inaccurate grading. Cleaning the screens thoroughly helps maintain optimal performance and ensures that the classifying process remains efficient and reliable.
Proper classifier maintenance also includes regular replacement of worn-out screens. Over time, screens can become worn and lose their classification accuracy. By monitoring the condition of the screens and replacing them when necessary, you can maintain consistent product quality and achieve precise grading.
Benefits of Proper Classifier Maintenance:
- Enhanced classifying accuracy and efficiency
- Consistent product quality
- Reduced downtime due to equipment failures
- Extended lifespan of the classifier
By following classifier maintenance guidelines, you can ensure that your classifying operations run smoothly and produce materials of the desired grades. Regular inspections, cleaning, and screen replacement are essential practices that contribute to efficient and reliable classifying processes.
De-dusting: Removing Fine Dust from the Production Stream
De-dusting is a crucial process that involves the removal of fine dust particles from powders to ensure optimal product quality. In industries such as food, pharmaceuticals, and minerals, the presence of dust can impact the integrity, purity, and safety of the final product. To effectively de-dust materials, centrifugal sifters and classifiers equipped with undersize screens are commonly used.
Implementing proper cleaning techniques is essential for maintaining efficient de-dusting operations and preventing material build-up. Regular disassembly and cleaning of internal components, such as screens, trays, and surfaces, help ensure the removal of dust and prevent the clogging of the sifter or classifier. By following these sifter and classifier cleaning techniques, you can enhance the performance and longevity of your equipment, and ultimately, improve product quality.
Key De-dusting Techniques:
- Regularly disassemble and clean internal components to remove dust buildup.
- Inspect screens for wear and tear, and replace them when necessary.
- Utilize appropriate cleaning solutions and techniques to effectively remove dust and contaminants.
- Implement a scheduled cleaning routine to prevent excessive dust accumulation.
By dedicating time and effort to de-dusting and maintaining your sifters and classifiers, you can ensure that your production stream remains free of fine dust particles, resulting in improved product quality and customer satisfaction.
Conclusion
Efficient sifter and classifier maintenance is essential for maximizing performance, reliability, and overall process efficiency. By implementing maintenance best practices such as regular inspections, cleaning, and troubleshooting, you can ensure the longevity of your equipment and minimize costly breakdowns.
Regular inspections allow you to identify any potential issues before they escalate, enabling timely repairs or replacements. Cleaning your sifters and classifiers on a regular basis removes accumulated debris and prevents material build-up, optimizing their efficiency and preserving product quality.
Furthermore, troubleshooting is a crucial aspect of maintenance that helps identify and address any operational challenges or inefficiencies promptly. By diagnosing and resolving issues promptly, you can maintain smooth operations and prevent production disruptions.
Remember, investing time and effort into efficient sifter and classifier maintenance not only extends the lifespan of your equipment but also contributes to consistent product quality and reliable process performance. Make maintenance a priority to ensure your sifters and classifiers are always in top shape.
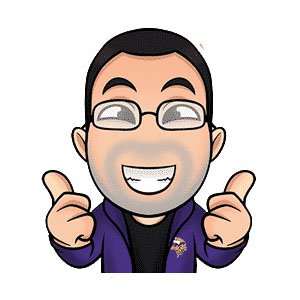
Meet Ryan Conlon, the passionate owner and driving force behind Pan for Treasure.
With an unwavering love for the art of gold panning, Ryan has transformed his enthusiasm into a thriving community hub for fellow treasure seekers. info@panfortreasure.com
A seasoned gold panning enthusiast, Ryan’s journey began with a simple pan and a dream, evolving into a deep appreciation for the history, geology, and thrill of uncovering precious metals.
Subscribe to Our Newsletter